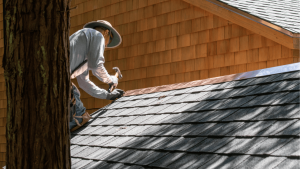
Roof flashing in Miami: Hurricane-Proofing your home’s weakest link
Understanding this vulnerability and investing in fortified flashing is not just a smart choice; it’s an essential defense against the persistent threats of South Florida’s climate.